Step Coupling Analysis and Electric Field Characteristics of HVDC Submarine Cables
Time: 2025-03-10 14:39:14
Source: Henan Province Jianyun Cable Co., Ltd.
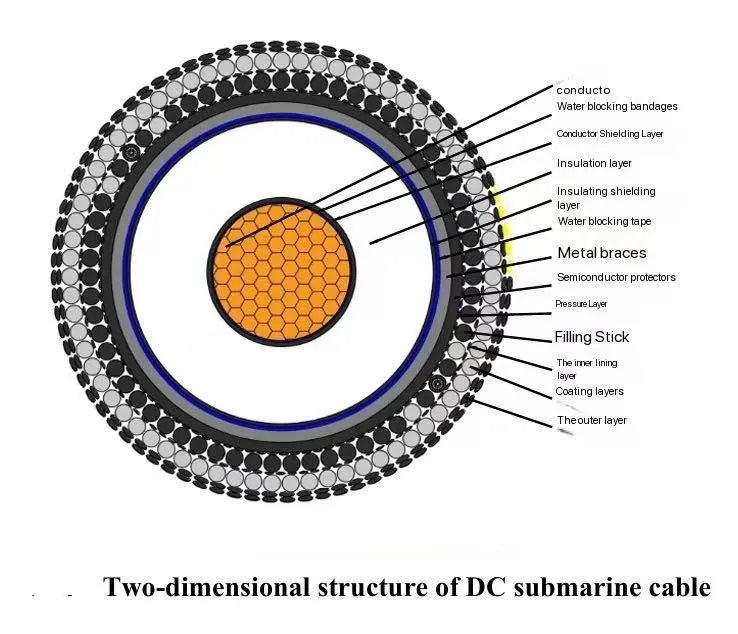
Introduction
High-voltage direct current (HVDC) submarine cables play a critical role in offshore wind power transmission, intercontinental power grids, and deep-sea energy projects. These cables require stable electrical insulation and reliable thermal performance to ensure efficient power delivery over long distances.
A key challenge in HVDC cable design is the electrothermal coupling effect, where temperature gradients affect the electric field distribution inside the insulation. This article explores step-by-step coupling analysis methods to model and optimize electric field intensity, temperature gradients, and space charge distribution in submarine cables.
Why is Electrothermal Coupling Important for HVDC Cables?
Challenges in HVDC Submarine Cable Operation
-
Heat generation and dissipation: Conductors generate heat under load, affecting insulation properties.
-
Electric field distortion: Temperature-dependent variations in conductivity can cause field intensity inversion, leading to insulation degradation.
-
Space charge accumulation: DC voltage operation leads to the build-up of charges inside the insulation, which can alter the electric field distribution and accelerate aging.
-
Modeling complexity: Traditional finite element analysis (FEA) methods require extensive computation time, making real-time optimization difficult.
Step Coupling Analysis: A More Efficient Approach
To improve computational efficiency, researchers have developed a step coupling analysis method, which separates thermal and electrical calculations into distinct steps:
-
Step 1: Calculate the temperature field under given operating conditions.
-
Step 2: Use temperature-dependent conductivity to determine electric field distribution.
-
Step 3: Analyze space charge dynamics based on field intensity and material properties.
By using COMSOL Multiphysics simulations, this method reduces calculation time while maintaining accuracy.
Finite Element Modeling for HVDC Submarine Cables
Key Cable Parameters
A ±400 kV, 2000 mm² cross-linked polyethylene (XLPE) insulated HVDC submarine cable was used for the study. The cable structure and material properties are outlined in the table below:
Component
|
Outer Radius (mm)
|
Thermal Conductivity (W/m·K)
|
Conductor (Copper)
|
53.2
|
400
|
Insulation (XLPE)
|
109.3
|
0.46
|
Metal Sheath
|
122.2
|
35.3
|
Armor Layer
|
159.8
|
58
|
Outer Sheath
|
166.8
|
0.25
|
Simulation Setup
-
Conductor load current: 1900 A (rated), varied from 10 A to 1910 A
-
Ambient temperature: 40°C
-
Boundary conditions:
-
Heat conduction: Between cable layers.
-
Heat convection: Outer sheath to surrounding environment.
-
Voltage source: ±400 kV DC applied to conductor.
Key Findings: Temperature and Electric Field Distribution
1. Temperature Gradient and Insulation Conductivity
-
Heat is primarily generated by conductor resistance (Joule heating).
-
Higher load currents lead to larger temperature gradients within the insulation, affecting conductivity.
Load Current (A)
|
Inner Insulation Temperature (°C)
|
Temperature Gradient (°C)
|
Conductivity Increase
|
10 A
|
40.0
|
0.0
|
Baseline
|
800 A
|
45.3
|
1.5
|
2×
|
1600 A
|
61.0
|
6.2
|
9×
|
1900 A
|
69.9
|
8.7
|
22×
|
➡ Conclusion: Temperature gradients significantly increase conductivity, altering the internal electric field.
2. Electric Field Intensity and Field Inversion
-
In low current conditions (≤10 A), the electric field follows a uniform capacitive distribution (Laplace-like field).
-
At higher currents (≥1585 A), a field intensity inversion occurs, shifting the peak electric field from the inner insulation layer to the outer surface.
-
This increases the risk of dielectric breakdown if the peak field exceeds 20 kV/mm.
Load Current (A)
|
Max Electric Field (kV/mm)
|
Field Location
|
10 A
|
17.5
|
Inner insulation
|
1200 A
|
16.3
|
Even distribution
|
1900 A
|
16.1
|
Outer insulation
|
➡ Conclusion: Field inversion at high currents can increase surface stress, requiring careful insulation design.
3. Space Charge Accumulation
-
DC cables accumulate space charge over time, leading to charge redistribution and local field enhancement.
-
At steady-state operation (≥30,000 s), the outer insulation accumulates more charge, increasing electrical stress on the outer sheath.
Load Current (A)
|
Space Charge Accumulation (C/m³)
|
Charge Distribution
|
10 A
|
0.469
|
Inner > Outer
|
1600 A
|
0.637
|
Uniform
|
1900 A
|
0.664
|
Outer > Inner
|
➡ Conclusion: Higher load currents shift space charge towards the outer insulation, increasing failure risk.
Engineering Recommendations for HVDC Submarine Cables
1. Optimizing Temperature Management
-
Improve insulation thermal conductivity to minimize temperature gradients.
-
Use heat-dissipating metal sheaths to enhance cooling.
2. Preventing Field Inversion
-
Select XLPE formulations with lower temperature-dependent conductivity variations.
-
Implement field grading layers to control voltage stress distribution.
3. Minimizing Space Charge Effects
-
Use nanocomposite XLPE materials to suppress charge injection.
-
Employ charge-trapping additives to limit space charge mobility.
Future Research Directions
-
Development of advanced XLPE composites with enhanced thermal and electrical stability.
-
Integration of real-time monitoring systems for early detection of insulation degradation.
-
Experimental validation of simulation models under long-term DC voltage conditions.
Conclusion
Step coupling analysis provides a powerful tool for optimizing HVDC submarine cable design. By decoupling temperature and electric field calculations, this approach improves computational efficiency and accuracy. The results demonstrate:
-
Significant temperature-dependent variations in insulation conductivity.
-
Field intensity inversion at high currents, leading to surface stress increases.
-
Space charge accumulation over time, affecting insulation reliability.
By implementing thermal management strategies, field grading techniques, and charge mitigation approaches, engineers can extend the operational life and reliability of HVDC submarine cables, ensuring safer and more efficient offshore power transmission.
References
-
Wang, D., Quan, Y., Guan, Y., et al. (2025). Step Coupling Analysis and Electric Field Characteristics of HVDC Submarine Cable. Wire & Cable, 68(1), 9-17. DOI: 10.16105/j.dxdl.1672-6901.20240169
-
Hanley, T. L., Burford, R. P., Fleming, R. J., et al. (2003). A General Review of Polymeric Insulation for Use in HVDC Cables. IEEE Electrical Insulation Magazine, 19(1), 13-24.
-
Li, S., Wang, X., Zhang, Y., et al. (2020). Analysis of Space Charge Distribution in High Voltage XLPE Insulated DC Cables. IEEE Transactions on Dielectrics and Electrical Insulation, 27(3), 947-955.