Electrothermal Coupling Analysis of Middle and Low-Pressure Composite Umbilical Cables in Winding State
Time: 2025-03-10 14:19:20
Source: Henan Province Jianyun Cable Co., Ltd.
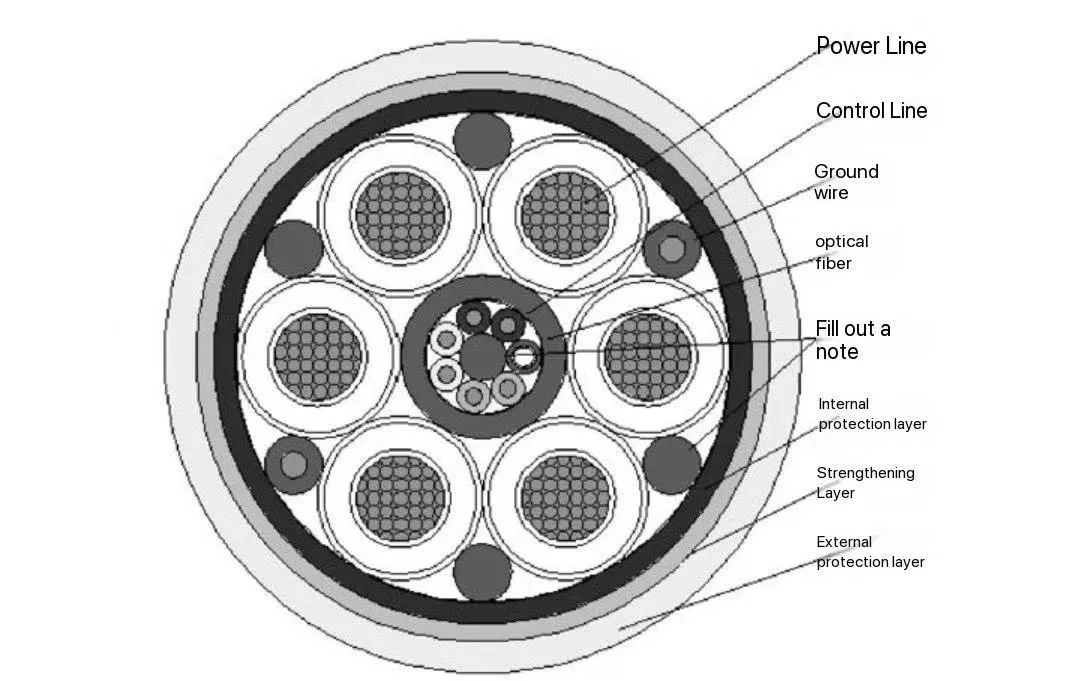
Introduction
Composite umbilical cables are widely used in offshore engineering, especially in subsea operations, remotely operated vehicles (ROVs), and dynamic power transmission systems. These cables often operate under high mechanical stress and thermal loads, making it crucial to understand their electrothermal behavior under different operational conditions.
When wound onto a winch system, umbilical cables experience temperature rise due to electrical current and mechanical compression, which can impact performance, safety, and longevity. This article explores the electrothermal coupling characteristics of composite umbilical cables in winding states, using finite element analysis (FEA) simulations to evaluate heat distribution and influencing factors.
Why is Electrothermal Analysis Important for Umbilical Cables?
Challenges in Umbilical Cable Operation
-
Thermal stress: High electrical loads cause heat buildup, affecting insulation performance.
-
Mechanical stress: Winding on a winch induces pressure and deformation, impacting thermal dissipation.
-
Safety concerns: Overheating can lead to insulation degradation and failure.
-
Load capacity: The thermal profile determines the cable's current-carrying capacity.
Understanding these factors helps optimize cable design and operational safety.
Finite Element Model for Heat Distribution Analysis
To evaluate temperature rise and heat dissipation in wound umbilical cables, researchers built a 2D electrothermal coupling model using finite element analysis.
Key Modeling Parameters
-
Cable type: Middle and low-pressure composite umbilical cable.
-
Conductor cross-section: 50 mm².
-
Materials:
-
Copper conductor (thermal conductivity: 400 W/m·K)
-
Cross-linked polyethylene (XLPE) insulation (10 W/m·K)
-
Polyurethane sheath (0.185 W/m·K)
-
Non-metallic armor layer (0.46 W/m·K)
-
Steel winch drum (76.2 W/m·K)
Component
|
Material
|
Thermal Conductivity (W/m·K)
|
Conductor
|
Copper
|
400
|
Insulation
|
Cross-linked polyethylene
|
10
|
Sheath
|
Polyurethane
|
0.185
|
Armor Layer
|
Non-metallic composite
|
0.46
|
Winch Drum
|
Steel
|
76.2
|
Simulation Setup
-
Modeling Assumptions:
-
Conductor load current: 128.3 A
-
Environmental temperature: 45°C
-
Steady-state thermal analysis
-
Boundary Conditions:
-
Heat conduction: Between cable layers and winch drum.
-
Heat convection: Between the cable outer surface and ambient air.
-
Heat sources: Electrical losses in the conductor.
-
Temperature Field Distribution:
-
Maximum heat accumulation occurs at the middle cable layers.
-
Maximum recorded temperature: 65°C (below the critical 90°C insulation limit).
Effect of Cable Arrangement on Heat Dissipation
Different cable winding patterns impact thermal performance. Three common arrangements were analyzed:
Arrangement Type
|
Description
|
Max Temperature (°C)
|
Heat Dissipation Effectiveness
|
Type 1
|
Alternating single and double layer
|
58.7
|
Moderate
|
Type 2
|
Uniform stacking per layer
|
58.4
|
Best
|
Type 3
|
Staggered winding
|
59.1
|
Least effective
|
➡ Conclusion: Uniform stacking (Type 2) provides the best heat dissipation, but Type 1 is easier to implement in practice.
Impact of Number of Cable Layers on Temperature
-
More layers increase heat accumulation due to reduced airflow.
-
A comparison of different layer counts (keeping total cable length constant):
Number of Layers
|
Cable per Layer
|
Max Temperature (°C)
|
7 Layers
|
5 turns/layer
|
58.7
|
5 Layers
|
7 turns/layer
|
57.8
|
4 Layers
|
9 turns/layer
|
56.4
|
➡ Conclusion: Fewer layers with more turns per layer improve cooling efficiency.
Effect of Winch Drum Sidewall Thickness
-
The thermal conductivity of the winch drum impacts cooling.
-
Simulations tested sidewall thickness from 10mm to 30mm.
Winch Sidewall Thickness (mm)
|
Max Temperature (°C)
|
10 mm
|
59.0
|
15 mm
|
58.8
|
20 mm
|
58.7
|
25 mm
|
58.5
|
30 mm
|
58.4
|
➡ Conclusion: Sidewall thickness has minimal effect on temperature. Winch design should prioritize structural strength rather than heat dissipation.
Key Findings and Recommendations
-
Electrothermal coupling analysis is essential for ensuring cable safety during winch operation.
-
Uniform stacking arrangements (Type 2) provide optimal heat dissipation.
-
Increasing turns per layer reduces overall temperature, improving cable performance.
-
Winch sidewall thickness has negligible impact on heat dissipation.
-
Finite element analysis (FEA) provides accurate and reliable predictions, guiding cable system optimization.
Future Research Directions
-
Real-time temperature monitoring for dynamic loading conditions.
-
Material innovations to enhance thermal dissipation.
-
Alternative cooling mechanisms for high-load applications.
Conclusion
Electrothermal analysis of umbilical cables in winding states provides critical insights for optimizing offshore cable systems. By leveraging finite element analysis, engineers can design safer, more efficient cable configurations, reducing failure risks and improving long-term reliability.
Understanding thermal behavior in different winding configurations enables better engineering decisions, ensuring optimal performance in subsea operations.
References
-
IEC 60287-1-1: Electric Cables - Calculation of Current Rating (2023).
-
Chen Z., Xue C., Niu X. et al. Electrothermal Coupling Analysis of Composite Umbilical Cable. Wire & Cable, 2025, 68(1):1-8. DOI: 10.16105/j.dxdl.1672-6901.20240159
-
Han X., Liu X. Cable Ampacity Correction Using Multi-Physics Field Coupling. Computer Simulation, 2023, 40(6):381-387.
-
Li H., Zhang Y. Simulation of Temperature Field in XLPE Cables Under Different Laying Conditions. Electric Power Engineering, 2023, 42(1):169-177.
-
Zhou Q., Yang T. Temperature Field Analysis of Pipe-Laid Cables Using Finite Element Method. Journal of Electric Power, 2023, 38(5):397-404.