Application of Electromagnetic Technology in Fault Location of Submarine Cables
Time: 2025-03-10 14:49:27
Source: Henan Province Jianyun Cable Co., Ltd.
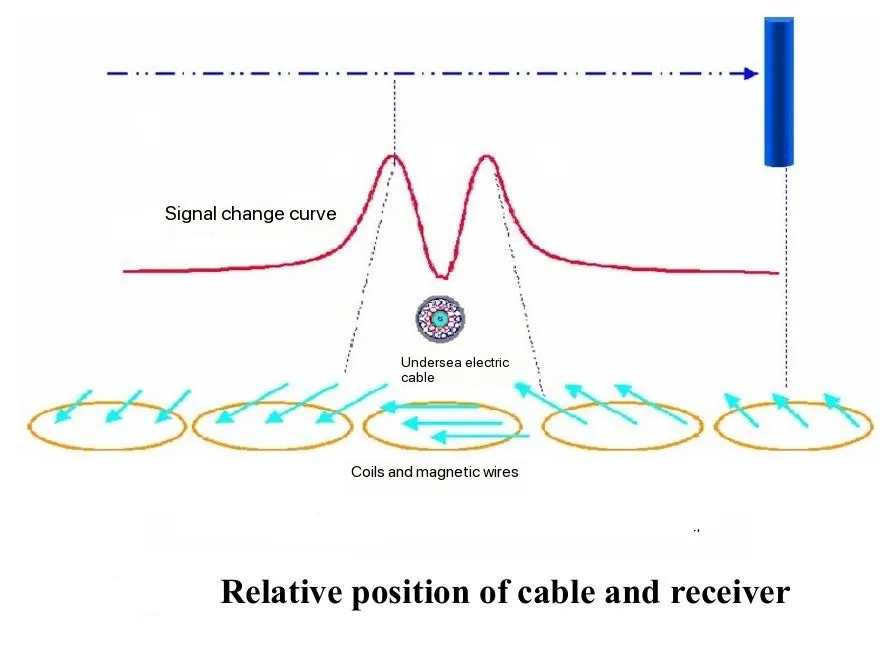
Introduction
Submarine power cables are critical components in offshore wind farms, intercontinental power transmission, and undersea communication networks. Due to their complex operating environments—subject to strong currents, seabed movements, and accidental damage from ships or marine life—faults in submarine cables can cause significant economic losses and power disruptions.
One of the biggest challenges in submarine cable maintenance is accurately locating faults. Traditional methods, such as time-domain reflectometry (TDR) and traveling wave techniques, have limitations in undersea environments. The electromagnetic (EM) method, based on electromagnetic induction principles, has emerged as an efficient, precise, and non-invasive alternative for fault detection.
This article explores the principles, implementation, and real-world case studies of electromagnetic fault detection technology, highlighting its effectiveness in improving submarine cable maintenance.
Why Electromagnetic Fault Detection?
Challenges in Locating Submarine Cable Faults
-
Harsh marine environments: Cables are buried under seabed sediments or exposed to corrosive seawater.
-
Interference from marine activities: Fishing, anchoring, and seabed infrastructure can complicate fault detection.
-
Limited access: Unlike overhead power lines, submarine cables cannot be visually inspected.
-
Complexity of cable networks: Offshore wind farms have multiple cable branches, making pinpointing faults more challenging.
Advantages of Electromagnetic (EM) Method
The electromagnetic fault location method works by injecting an alternating current (AC) signal into the faulty cable and detecting the magnetic field variations around the fault location. Compared to traditional methods:
-
Higher Accuracy: EM techniques provide precise location data down to meters.
-
Non-invasive: No need to physically access the cable, reducing inspection time and costs.
-
Works in complex environments: Can locate faults even in areas with high electromagnetic noise.
Electromagnetic Fault Location Principles
1. Theory of Electromagnetic Induction
According to Faraday’s Law, an alternating current (AC) flowing through a conductor generates a magnetic field, which can be detected using specialized receivers.
The magnetic field strength (B) at a distance X from the cable is given by:
B=μI2πXB = \frac{\mu I}{2\pi X}
Where:
-
B = Magnetic field intensity (Tesla)
-
I = Current in the conductor (Amperes)
-
μ = Magnetic permeability (H/m)
-
X = Distance from the cable (m)
2. Fault Detection Mechanism
-
A low-frequency AC signal (25–150 Hz) is injected into the cable.
-
The faulty section creates a loop with seawater, altering the magnetic field pattern.
-
An electromagnetic sensor array detects the disturbance, pinpointing the fault location.
Case Study: Offshore Wind Farm Cable Fault Detection
1. Fault Overview
A 35 kV submarine optical-electric composite cable in an offshore wind farm developed a fault 0.35 km from the offshore substation. The cable was buried in shallow water (15m depth), making traditional detection methods ineffective.
Parameter
|
Value
|
Voltage Level
|
35 kV
|
Cable Length
|
5.5 km
|
Water Depth
|
15 m
|
Fault Distance
|
0.35 km from substation
|
2. Key Steps in Electromagnetic Fault Location
Step 1: Signal Injection
-
The cable was de-energized, and a low-frequency AC signal (150 Hz, <300V) was injected at the offshore wind turbine terminal.
-
The far end of the cable was grounded, ensuring current flow.
Step 2: GPS-Integrated Magnetic Field Scanning
-
An autonomous underwater vehicle (AUV) equipped with an electromagnetic sensor scanned the seabed.
-
The sensor recorded magnetic field variations and synchronized with GPS coordinates.
Step 3: Magnetic Field Analysis
-
The first scan showed no significant anomalies up to 2.00 km.
-
At 0.35 km, the magnetic field dropped suddenly, indicating a high-resistance fault.
Step 4: Confirmation and Localization
-
The insulation resistance of the faulty cable was measured at 468 kΩ, confirming a partial breakdown.
-
After further testing, the fault position was determined within ±3 meters.
3. Final Results
-
The electromagnetic method successfully located the fault in less than 24 hours.
-
Compared to traditional methods (which can take several days), this approach reduced diagnostic time by over 60%.
-
The fault was later confirmed as mechanical damage from seabed movement.
Comparison of Fault Location Methods
Method
|
Principle
|
Accuracy
|
Limitations
|
Time-Domain Reflectometry (TDR)
|
Measures signal reflection time
|
±100 m
|
Less effective in high-resistance faults
|
Traveling Wave Method
|
Analyzes wave propagation in the cable
|
±50 m
|
Requires synchronized high-speed data acquisition
|
Electromagnetic Method (EM)
|
Detects induced magnetic fields around faults
|
±3 m
|
Requires external AC signal injection
|
Optical Time-Domain Reflectometry (OTDR)
|
Uses light pulses to locate optical fiber faults
|
±5 m
|
Only applicable to optical cables
|
➡ Conclusion: The electromagnetic method offers the best balance of accuracy, speed, and reliability for submarine cable faults.
Key Takeaways and Recommendations
-
Electromagnetic fault detection is highly effective for submarine cables, providing meter-level accuracy.
-
Integrating GPS and real-time data processing enhances fault location precision.
-
Future improvements should focus on:
-
Automating sensor deployment using AI-driven AUVs.
-
Developing machine learning algorithms for faster data analysis.
-
Improving signal penetration for deep-sea applications.
Future Research Directions
-
Enhancing resistance to electromagnetic interference (EMI) from offshore power stations.
-
Testing in deeper waters (>1000m) for ultra-deep-sea cable applications.
-
Real-time fault monitoring using IoT-connected EM sensors.
Conclusion
The electromagnetic method provides a game-changing approach to submarine cable fault detection, offering:
✔ High accuracy (within ±3m)
✔ Non-invasive testing (no need to physically access the cable)
✔ Rapid fault location (reduces downtime by over 60%)
As offshore energy systems expand, improving fault detection technologies will be crucial for maintaining efficient and resilient power networks. The electromagnetic method, combined with AI, IoT, and autonomous underwater robotics, is set to become the gold standard for submarine cable diagnostics.
References
-
Li, L., Zhou, F., Wang, T., Xu, Y., Ning, X., Qian, H. (2025). Application of Electromagnetic Technology in Fault Location of Submarine Cables. Wire & Cable, 68(1), 18-24. DOI: 10.16105/j.dxdl.1672-6901.20240078
-
Zhao, J. & Chen, Z. (2011). Research on Submarine Cable Projects at Home and Abroad. East China Electric Power, 39(9), 1477-1481.
-
Sun, Z., Li, N., Qi, L. (2024). Traveling Wave Method Fault Location of Offshore Wind Power Submarine Cables Based on SIMULINK Simulation. Wire & Cable, 67(4), 37-41.
-
Tang, K., Wang, S., Liu, S. (2019). Emergency Repair of Offshore Oilfield Submarine Cables. China Petroleum and Chemical Standards, 39(7), 29.